|
Several firings of the Large Fred Olsen Kiln at ICS in Hungary |
|
|
Jacob begins stacking  |
a days stacking completed 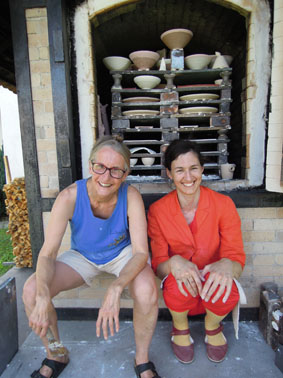 |
Early rising at 2am to begin firing |
|
The first fire box is underway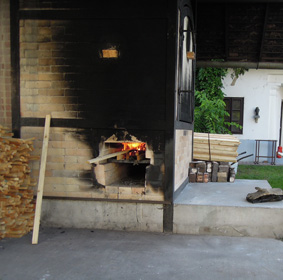 |
Enico stocking at temp1200 deg.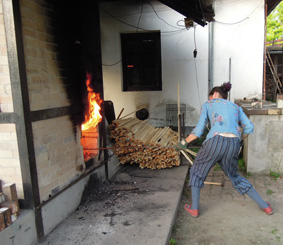 |
Night time flame 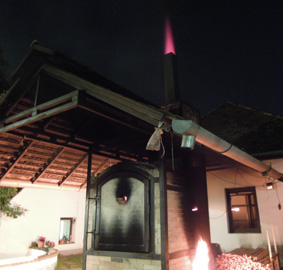 |
|
Jacob and Klari always smiling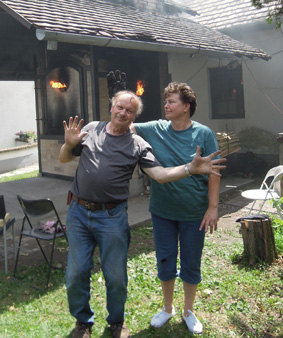 |
After 16 hours firing
at 1280 degrees, the kiln is sealed.

|
Klari and me.
Without the help of her and Jacob
and all the team, I couldn't do it. |
|
 |
The firing log shows what happened when and what we did. Very important for future firings.
We now wait 2 to 3 days for the kiln to cool down and we can open it up. |
Enico ..Relaxed exhaustion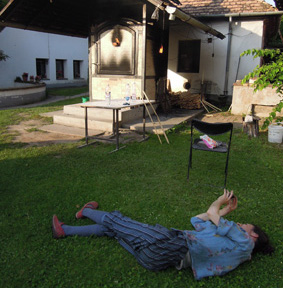 |
|
3 days later the kiln can be opened 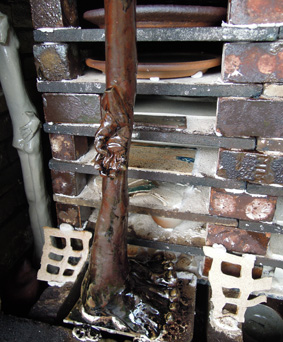 |
Jacob begins unpacking |
Sleeping beauty awakes |
|
 |
The use of shells in wood firing
As ash is a nauiral glaze all pieces in wood firing need to be held off the shelves. Normally this is done with wadding. Shells however have the amazing property of supporting even heavy pieces, leaving interesting marks, yet once touched after firing they turn to powder in your hands. |
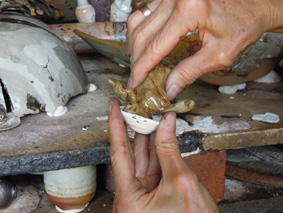 |
|
 |
Klari and Jacob with their Kiln Gods.Every firing they are made for luck and to thank them.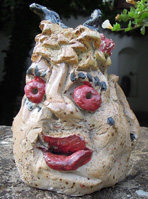 |
My seagull god in the cabinet of the Gods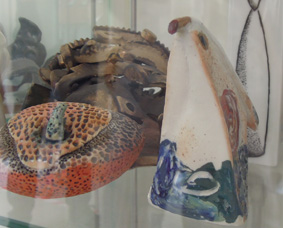 |
|
|
|
|
|
Making of works |
|
|
|
|
|
|
Carving a cruved piece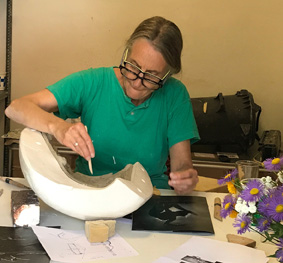 |
A slab is rolled, the landscape pressed into it, then gently wrapped around the form. Slowly the body shape is established by pushing and stretching the clay.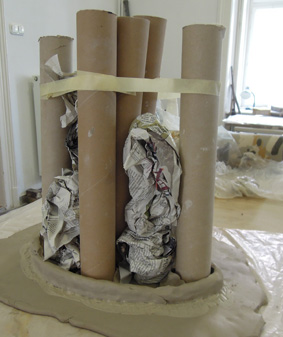 |
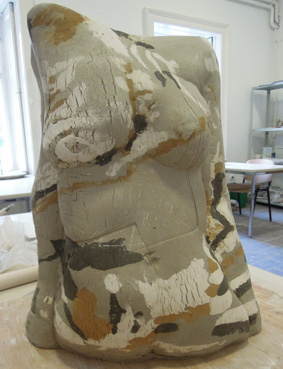 |
|
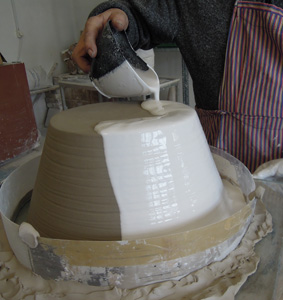 |
In making a mould for the lithophane lamp base, Enico threw the clay bowl for me, then a mould was made into which slip porcelain is poured, then finished off slowly by hand to form the light and mounting structure. 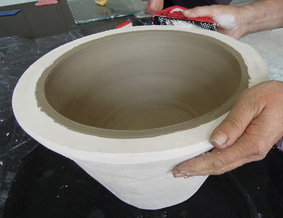 |
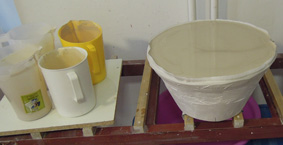
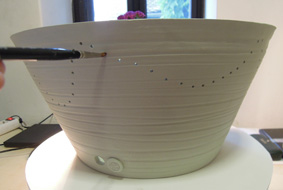
|
|
Lithophane: the design is carved into a plaster slab. Bone China slip is then poured in a thin layer over it. The resulting piece is cleaned then fired. With the lighting underneath the negative image becomes a positive. |
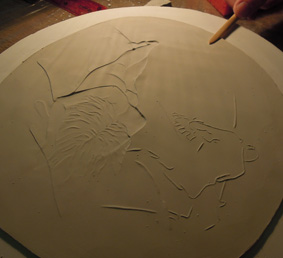 |
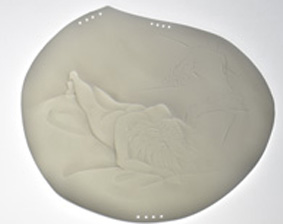 |
|
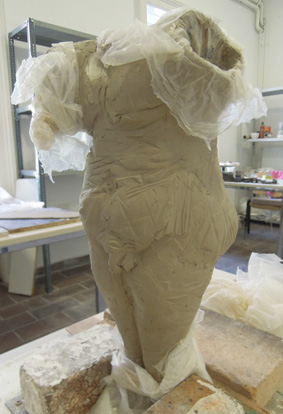 |
Each sculpture is built up from the feet adding coils of clay. The only tool I use is a piece of 4x2 wood to and my hands to push, bash and cajole the clay. 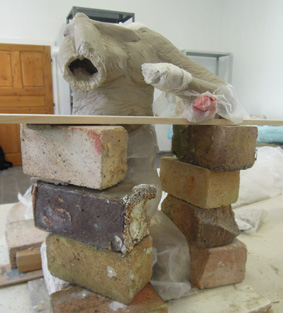 |
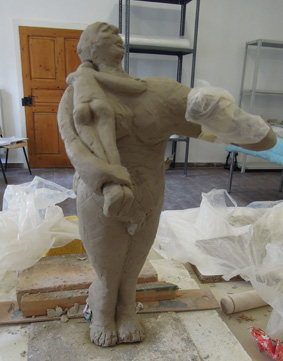 |
|
|
|
|
|
Several firings of the Fred Olsen Fast Fire Kiln at ICS in Hungary |
|
|
|
|
|
|
Firing with Adam |
First one fire box is lit, later the second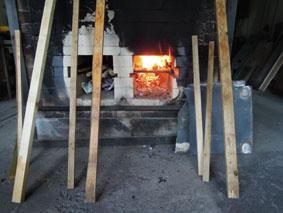

|
 |
|
Before |
Hanging of the firing cone. As a temperature is reached the cone bends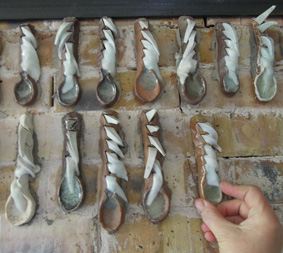 |
After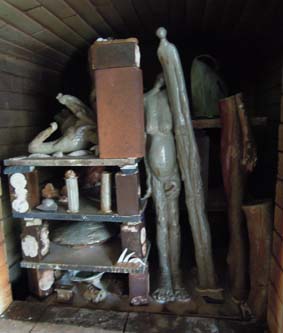 |
|
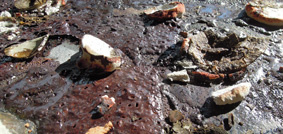
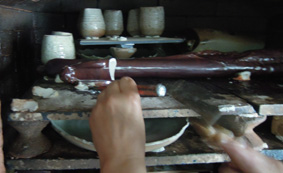
|
A successful firing often has its accidents and a glaze running, ruining a shelf, requiring forced extracting of the sculpture followed later with its rebuilding, is part of the uniqueness.  |
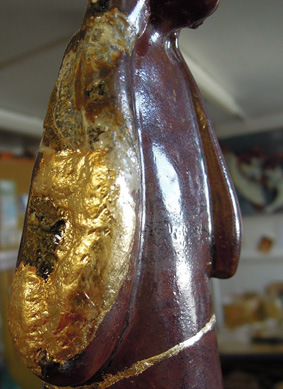 |
|
|
|
|
|
Raku Firing at ICS in Hungary |
|
|
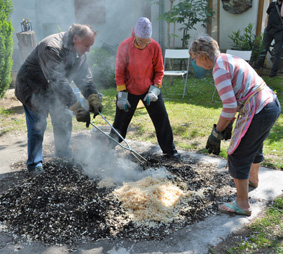 |
Sue and I examine the results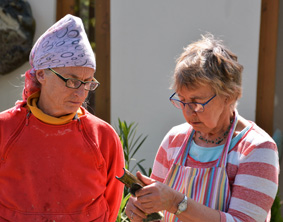 |
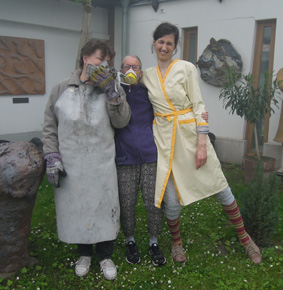 |
|
 |
< Enico unloading the oil raku
Not ideal for the face mask!! OR??
> then the reward !!
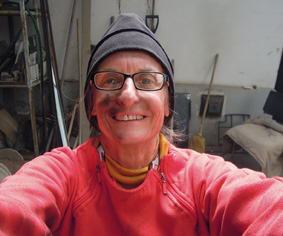
|
 |
|
|
|
|
|
Firing my larger gas kiln at home |
|
|
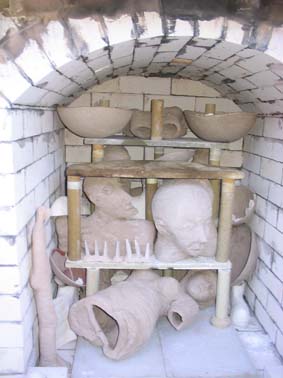 |
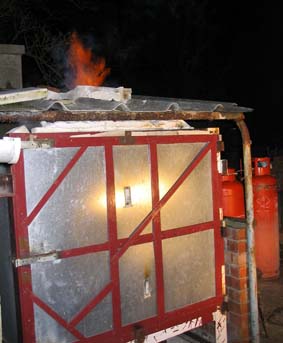 |
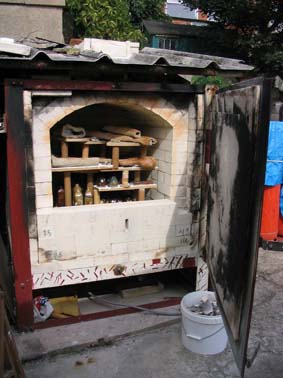 |
|
|
|
|
|
Firing the Anagama kiln at Rufford |
|
|
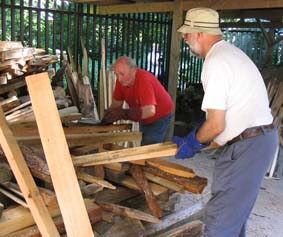 |
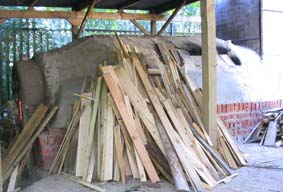 |
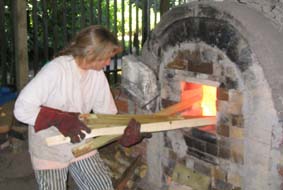 |
|
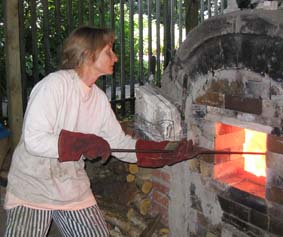 |
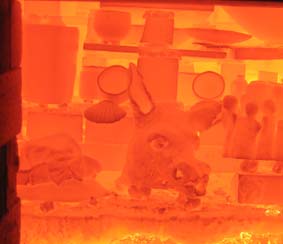 |
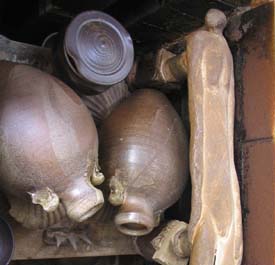 |
ALL HOT, THIRSTY REWARDING WORK |